
You might have to change up the coordinates a few times to get it right, but if you're making the EOT in solidworks, you can make a new assembly and import the entire EOT to re-do the coordinates.
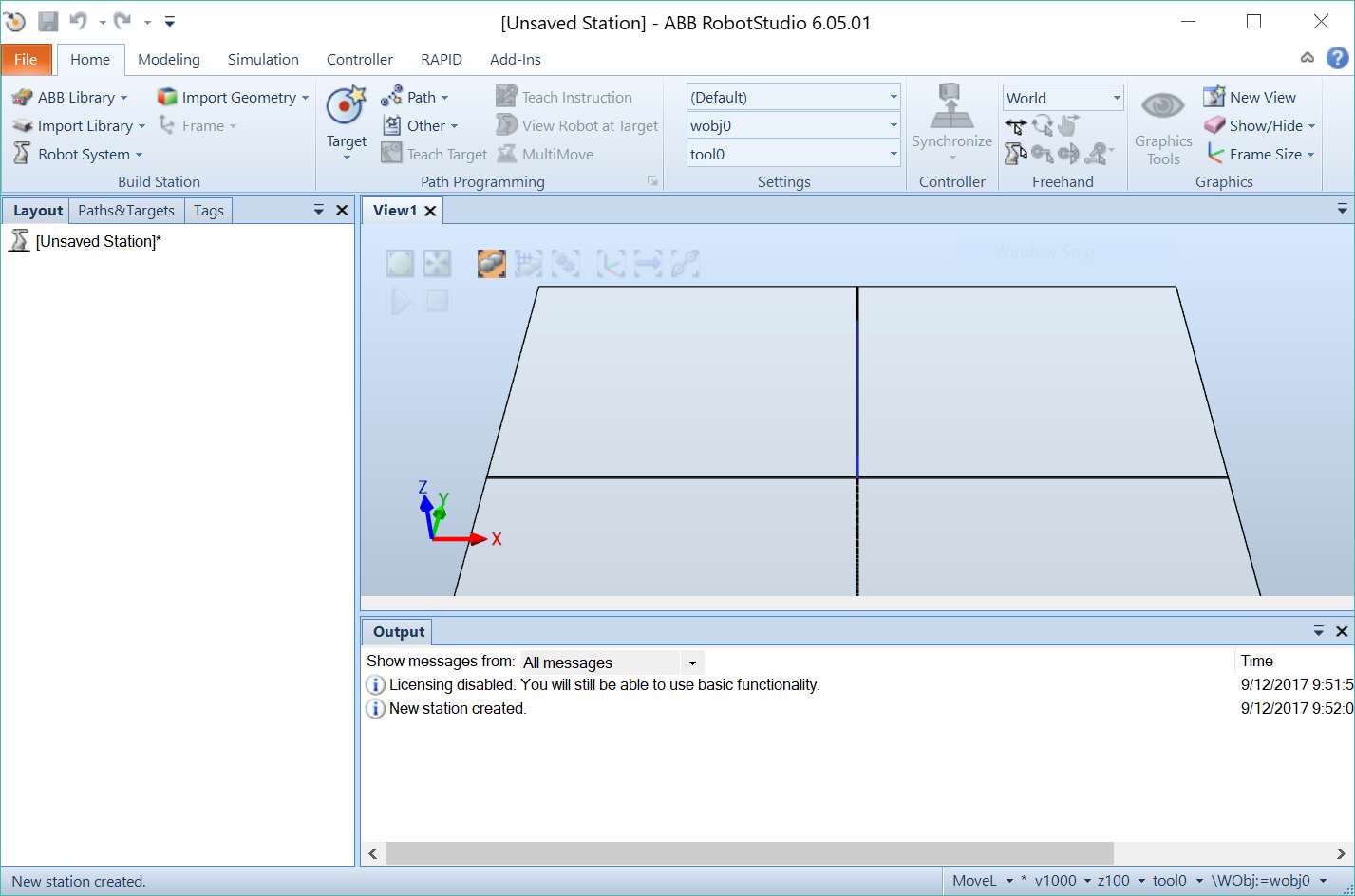
Then you can tell the part to be attached to the robot, and it will snap to the end of the robot nicely. Make sure that the EOT has the coordinate system where you want it to attach to the robot before you import that part into robot studio. You might have to rotate the target axis, or even the tool axis if most of your targets are pointing the same direction. The tool axis will fall onto the target axis exactly, lining up x, y and z. It is also important to look at the target axis. When creating targets, make sure you just click approximately where you want the EOT to go to on your nest, then you can offset that target to the actual desired location (let's be honest, once you are actually programming the robot, you will have to re-teach several points anyways). what should I be doing instead? How can I make my life easier here? Jogging is both tedious in a CAD envireoment not 'perfect' positing either.
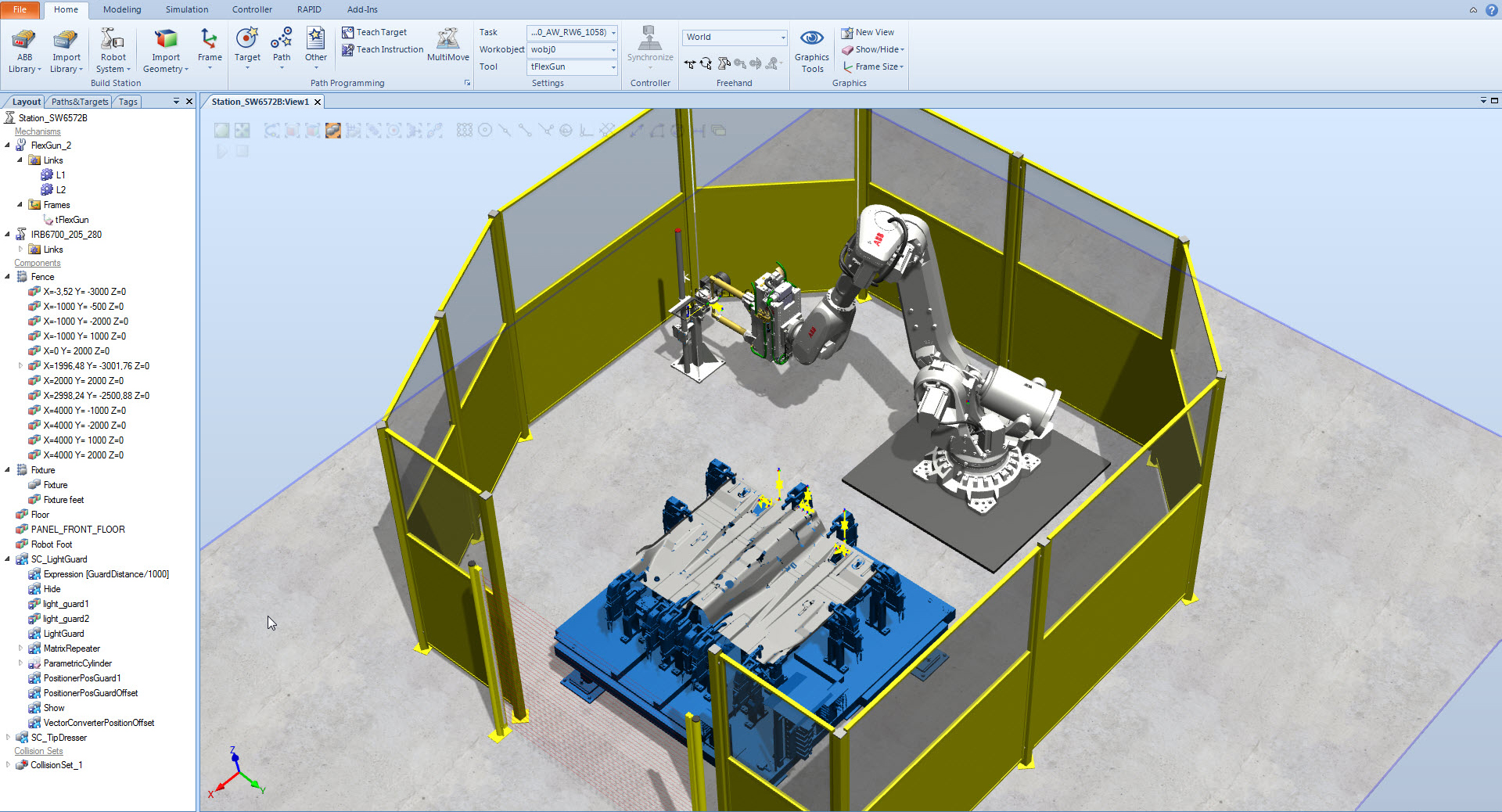
I'm not sure what to do with WorkObj0 or Tool0, a little confused about UCS (it's been useful a bit, but confusing). I've tried "attaching" and it ends up exploding my gripper (the parts attach but the tool stays where it was). It seems ok to teach a profile for a welder (most of the demos I've watched), but what about picking with a gripper? I have the TCP taught on the Gripper "Tool" and I have a Nest where I can figure out where the TCP should line up, but it seems awfully awkward to just make the robot snap-to the part! What's the fastest way to teach RobotTargets? Knowing that would really make my life easier.
#Abb robotstudio snap tcp to point software#
I feel like the software has the potential to be way more user-friendly, but has about a dozen different ways to do the same thing, which makes it horribly confusing for greenies. I'm brand new to Robot Studio 6.0.4 using an IRC5 4600. Please click "report" on spam Related sub-reddits: (*) At mods' discretion, certain self-promotion submissions from people who contribute to this sub in other ways may be allowed and tagged with the "Self-promo" flair
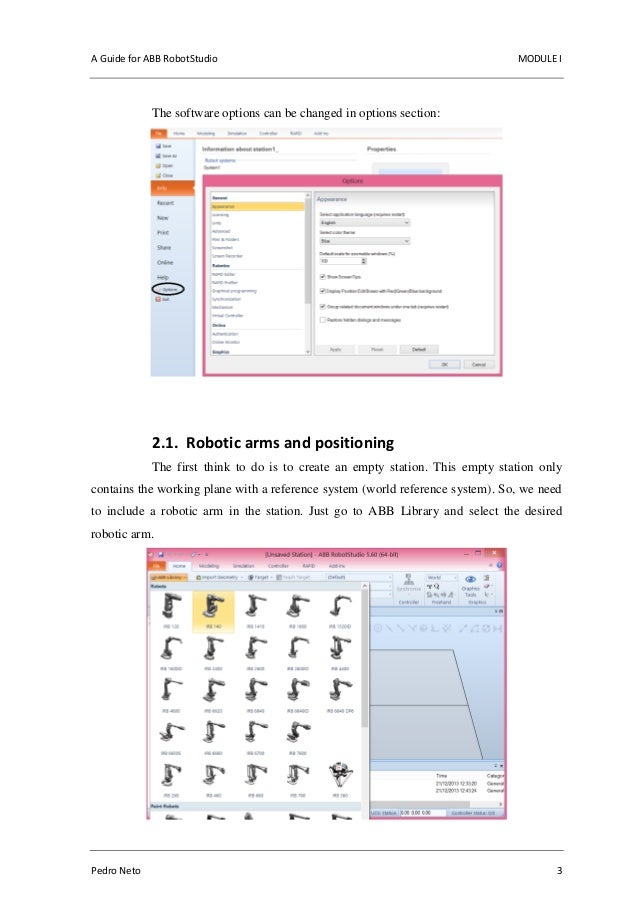
